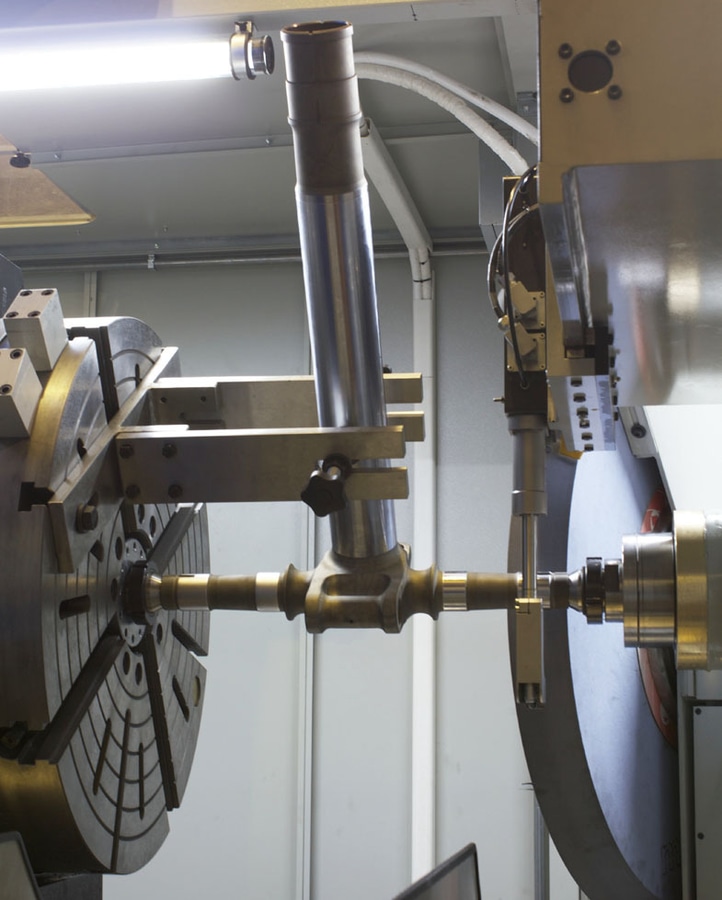
#Industry News
The best landing gear grinding solutions
Aerospace Report
Although the Covid-19 health emergency tests the entire sector, the international aviation industry, direct and indirect EOM and certified subcontractors, continues the important technological developments with innovations for all components and manufacturing processes used for the construction of increasingly efficient aircraft. For machine tool suppliers, in particular for finishing machines such as grinding machines, aerospace also means working very expensive single pieces, following strict production procedures with special work cycles that guarantee traceability and above all "zero defects" on the final pieces; the aerospace does not admit errors!
In this context, among the manufacturers of cylindrical grinders accredited for the aerospace industry, the Italian AZ SpA of Thiene (VI) has been able to achieve worldwide leadership success thanks to the high quality and performance levels of its products, the result of a high professionalism and engineering creativity able to grasp and often anticipate market demands. The aeronautics and aerospace sector have AZ SpA, a technological partner capable of offering numerous specific and very flexible grinding solutions with a high innovative content. AZ has an impressive range of grinding solutions designed specifically for the aerospace industry called "AZ Aerospace" for the manufacture and maintenance of components of aircraft engines and landing gear. AZ grinding machines are all customizable, energy efficient, safe, reliable and comply with Industry 4.0 requirements.
The numerous lines available are developed with the range AKP for external landing gear grinding machines with gap bed, GSB for internal landing gear grinding machines, LBC for landing gear orbital grinding machines for external and internal diameters, RU and RUG for universal grinding machines for external and internal diameters. Among the numerous high-precision grinding solutions of AZ SpA, the new AKP and GSB range have recently been renewed and made even more flexible and performing.
The AKP range for external grinding and GSB for internal grinding, have been designed as specific grinding machines for the landing gear of aircraft of various sizes and types. On AKP range, the presence of the gap bed on the base of the machine allows the complete machining of the components that require a large rotation diameter. In fact, the gap bed allows a max swing on the gap up to 3,600 mm with a swing over table up to 1,200 mm for workpiece length up to 5,000 mm.
On GSB range the grinding wheel moves on base by ball screw system and linear
guideway and allow internal grinding process, face grinding and taper grinding.
The maximum internal grinding diameter is up to 350 mm for workpiece length up to 3,000 mm. Common to both range, the machine base has been designed with FEM analysis and is made of thermally stabilized cast iron that guarantee an exceptional absorption of vibrations, great machine rigidity, stiffness and high dynamic performance. The grinding wheelhead, mounted on a rigid structure, is available in different configurations, straight, angular with manual or automatic B-Axis rotation which is driven by an integrated torque motor and can be equipped with a plurality of spindles for external and internal grinding processes. Silicon carbide, corundum, CBN and diamond grinding wheels can be used which allow to grind all aerospace materials, metals and their alloys including chromium and in particular those subjected to the most innovative systems for
thermal spray techniques, such us H.V.O.F. (High Velocity Oxygen Fuel). Based on the type of machine chosen, the headstock is designed to use different clamping
systems in accordance with the specific workpiece. The headstock can swivel manually or automatically and uses Morse cone or Asa centering system. The tailstock is equipped with conicity (taper) adjustment with continuous control of the force between centers. Numerous integrated grinding wheel dresser systems are available with diamond flarin cup wheel, diamond electroplated wheel and automatic fixed points or with single point diamond for internal wheel dresser.
The grinding process has some functions to give to the operator few automatic and safe working cycle such us Electronically variable spindle speed, GAP control, Dressing control, CRASH control and control of diameters from CNC.
There are also innovative solutions for factory integration. Wikicam is a monitoring system that allows to control remotely some parameters of the CNC machine. There is also a live video streaming solution built-in, to monitor what the machine is doing in real-time. The connection to the builder's headquarter is made by a high-strength secure encryption algorithm, using a VPN. The machine can be supplied with different measurement systems like absolute in-process measuring, in-process diameter measuring with fork and external measuring with double touch. Also motors, drives, as well as machine mechanisms and
applied CNCs, are selected among the best brands in the world.
The design creativity of AZ allows the creation of product lines, like the new AKP and GSB grinding machines, among the most sophisticated on the market today.
AZ SpA exhibits at the German Grindtec fair in Augsburg, November 10-13, at Hall 5 Stand 5094 where AZ engineers are available to illustrate all the technical characteristics and provide all information on the new AZ-Aerospace range.