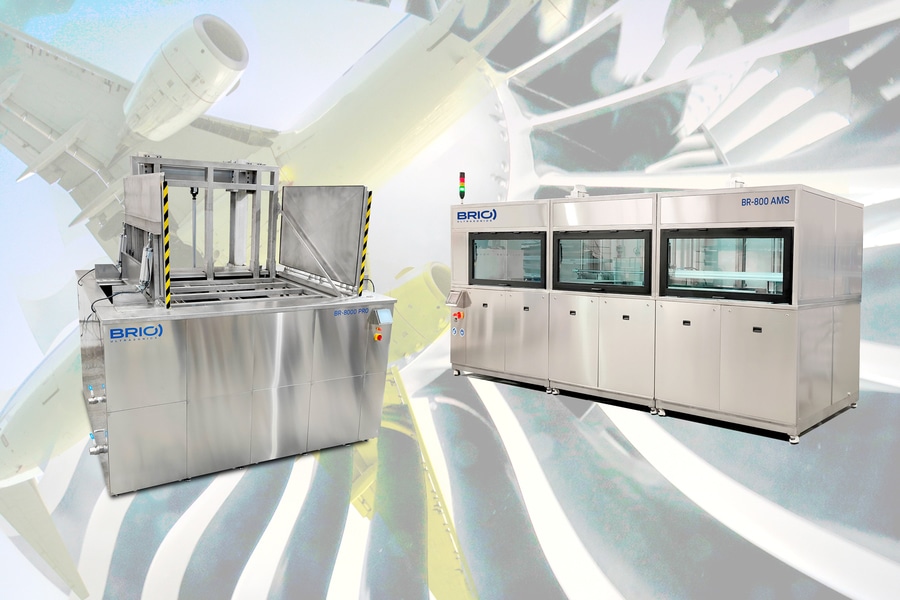
Vedi traduzione automatica
Questa è una traduzione automatica. Per vedere il testo originale in inglese cliccare qui
#News
{{{sourceTextContent.title}}}
Vantaggi dell'investimento in macchine per la pulizia a ultrasuoni BRIO per l'industria aeronautica
{{{sourceTextContent.subTitle}}}
L'investimento in macchine per la pulizia a ultrasuoni BRIO ottimizza i processi di pulizia e manutenzione e offre significativi ritorni a lungo termine
{{{sourceTextContent.description}}}
L'industria aeronautica richiede i più elevati standard di pulizia e manutenzione per garantire la sicurezza, l'efficienza e la durata dei suoi componenti. In questo contesto, la tecnologia di lavaggio a ultrasuoni è diventata una soluzione indispensabile per rimuovere efficacemente i contaminanti dai componenti dell'aviazione. Investire in macchine per il lavaggio a ultrasuoni non solo ottimizza i processi, ma offre anche significativi ritorni a lungo termine.
BRIO Ultrasonics è specializzata nella progettazione e produzione di soluzioni di lavaggio a ultrasuoni adatte alle esigenze del settore aeronautico. Le nostre apparecchiature combinano innovazione, efficienza energetica e sostenibilità per offrire risultati superiori nella pulizia di componenti critici. Attualmente, aziende come ITP Aero, Rolls Royce, Aerospace Engineering Group e Airgrup dispongono di macchine BRIO per i loro processi di manutenzione e produzione di componenti aeronautici. Con oltre 30 anni di esperienza, garantiamo soluzioni personalizzate che ottimizzano la manutenzione e prolungano la vita dei componenti, assicurando ai nostri clienti il miglior ritorno sugli investimenti.
- Come funziona una macchina per la pulizia a ultrasuoni dei componenti aeronautici
Le macchine per il lavaggio a ultrasuoni utilizzano onde acustiche ad alta frequenza per generare cavitazione acustica in un mezzo liquido. Questo fenomeno consiste nella formazione e nel collasso di microbolle che liberano in modo uniforme ed efficiente lo sporco, gli oli, i carboni, i polimeri e altri detriti aderenti alle superfici delle parti aeronautiche. Se volete saperne di più sul funzionamento di una macchina per la pulizia a ultrasuoni, potete consultare il nostro articolo sul blog.
Questo metodo è particolarmente efficace per i componenti critici degli aeromobili, come turbine, scambiatori di calore, impianti idraulici e parti strutturali, dove la pulizia convenzionale non è sufficiente a rimuovere i detriti incastrati in geometrie complesse.
- Vantaggi dell'utilizzo di macchine per la pulizia a ultrasuoni per l'industria aeronautica
- Maggiore precisione di pulizia
Le macchine per la pulizia a ultrasuoni rimuovono lo sporco nelle micro-cavità, nei condotti interni e nelle geometrie complesse senza la necessità di smontare le parti, garantendo una pulizia profonda e uniforme.
- Riduzione dei tempi di manutenzione
Automatizzando il processo di pulizia, i tempi di fermo degli aeromobili e delle apparecchiature si riducono significativamente, migliorando la produttività delle aziende del settore.
- Risparmio sui costi operativi
L'uso di soluzioni di pulizia riutilizzabili e la riduzione del consumo di sostanze chimiche riducono al minimo i costi rispetto ai tradizionali metodi di pulizia manuale o con solventi.
- Riduzione dell'usura e maggiore durata dei componenti
La pulizia a ultrasuoni non causa abrasione o usura dei componenti, preservandone le proprietà meccaniche e prolungandone la vita utile, riducendo la necessità di frequenti sostituzioni.
- Conformità alle normative e agli standard di qualità
Questo sistema di pulizia soddisfa i rigorosi standard dell'industria aeronautica, come quelli stabiliti dalla FAA e dall'EASA, garantendo che le parti siano prive di contaminanti prima della reinstallazione.
Investire in macchine di lavaggio a ultrasuoni per l'industria aeronautica è altamente conveniente, in quanto migliora l'efficienza della manutenzione, riduce i costi operativi e garantisce una pulizia ottimale senza danneggiare i componenti. In un settore in cui sicurezza e precisione sono essenziali, questa tecnologia si consolida come soluzione indispensabile per soddisfare i più elevati standard di qualità ed efficienza.