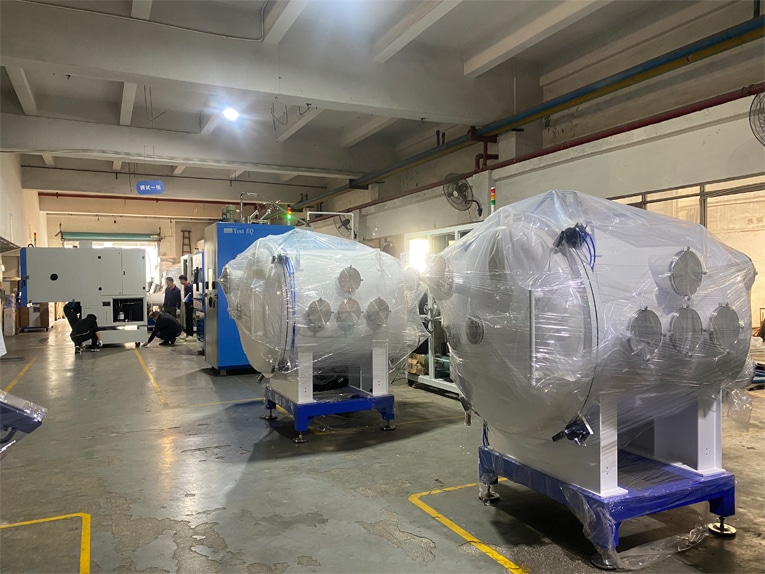
#Industry News
TVAC Chambers Revolutionize Cleaning Processes in Lithography Machine Production
Why Thermal Vacuum Chambers Are Essential in Lithography Production
In the highly precise world of semiconductor manufacturing, maintaining ultra-clean components is critical to ensuring optimal performance of lithography machines—the cornerstone of chip production. Thermal Vacuum Chambers (TVAC Chambers) play a pivotal role in this process, enabling advanced cleaning and outgassing treatments that meet stringent international standards.
Modern lithography machines, such as those produced by industry leaders like ASML, require components with ultra-low contamination levels to prevent defects in nanoscale chip patterning. Residual organic materials, particles, or outgassing from metal surfaces can disrupt vacuum integrity, leading to production delays and yield losses.
Thermal Vacuum Chambers address these challenges by:
A. Removing Organic Contaminants: High-temperature vacuum environments (up to 300°C) ensure complete elimination of hydrocarbons, solvents, and residues from stainless steel, titanium, and aluminum alloy components;
B.Reducing Outgassing: TVAC systems achieve <1×10⁻⁷ Torr vacuum levels, critical for preventing gas desorption that could interfere with EUV (Extreme Ultraviolet) lithography processes;
C.Enhancing Surface Adhesion: Post-cleaning, parts exhibit superior bonding with photoresist coatings, crucial for precise pattern transfer in DUV (Deep Ultraviolet) and EUV lithography;
Meeting International Standards with Advanced TVAC Technology:
Our Thermal Vacuum Chamber Testing solutions comply with:
ASTM E1559: Outgassing performance validation for semiconductor-grade cleanliness.
ISO 14644-1: Ensuring Class 1-9 cleanroom compatibility for particle-free surfaces.
SEMI Standards: Guaranteeing compatibility with wafer handling and optical component requirements.
Key technical parameters of our Thermo Vacuum Chamber systems include:
✔ Temperature Range: -70°C to +300°C (with rapid thermal cycling for stress testing)
✔ Vacuum Level: 10⁻⁷ Torr (UHV) to 10⁻⁹ Torr (XHV) for high-purity applications
✔ Gas Purge Options: N₂, Argon, or O₂ plasma cleaning for specialized surface treatments
✔ Uniform Heating: ±0.5°C temperature stability to prevent thermal stress on delicate optics
Applications in Lithography Machine Manufacturing
1.Optics & Mirror Cleaning: EUV lithography mirrors require ultra-clean surfaces to minimize light scattering. Our Heat Vacuum Chamber ensures particle-free optics through controlled thermal desorption.
2.Wafer Stage Degassing: Prevent micro-contamination in high-precision wafer alignment systems by removing adsorbed gases from mechanical components.
3.Photoresist Curing & Hard Baking: Some advanced resists require low-pressure thermal curing, achievable in our Vacuum Test Chamber for defect-free patterning.
Future-Proofing Semiconductor Manufacturing
As chipmakers push toward sub-3nm nodes, the demand for ultra-clean, low-outgassing components will only grow. Our Thermal Vacuum System solutions are designed to meet these evolving challenges, ensuring higher yields, reduced downtime, and compliance with next-gen semiconductor standards.
For more details on how our TVAC Chambers can optimize your lithography production line, contact us today.